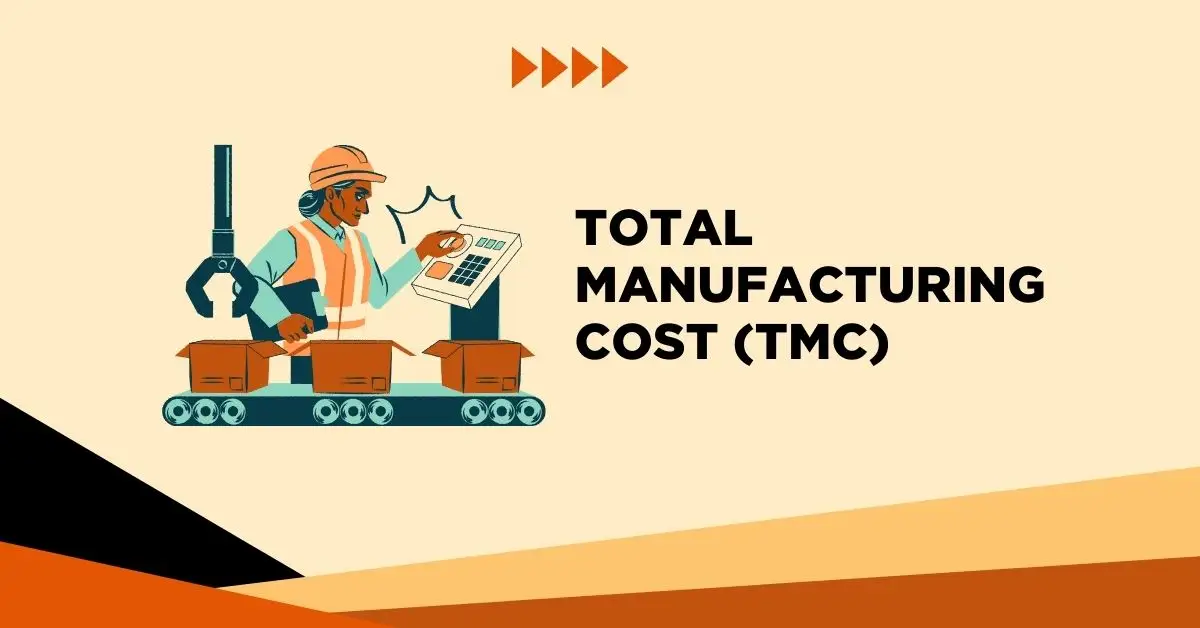
Total Manufacturing Cost: Formula, Calculation & Ready-to-Use Template
Are your manufacturing costs eating into your profits without you even knowing it? The total manufacturing cost (TMC) is important for any business engaged in productive operations that sell physical goods. The concept presents a clear and whole picture of what it takes to manufacture your products from raw materials to labor to overhead expenses.
TMC is an important financial metric to track. Actually, it's the foundation for setting competitive prices and determining your actual profitability. Moreover, TMC is essential to identify opportunities that help streamline operations. Once you know your true costs, pricing strategies, production methods, and areas for cost-cutting efforts make themselves known.
Key Takeaways
- Understand what total manufacturing cost (TMC) is and its formula.
- Learn how to calculate TMC with a practical example.
- Utilize our TMC calculator and a sample template to simplify things.
- Know the difference between TMC and cost of goods manufactured (COGM).
What Is Total Manufacturing Cost (TMC)?
TMC is simply the total money you spend to make your products. It's like adding up every dollar that goes into creating what you sell. It involves everything from material procurement to wages and utility bills for your production line.
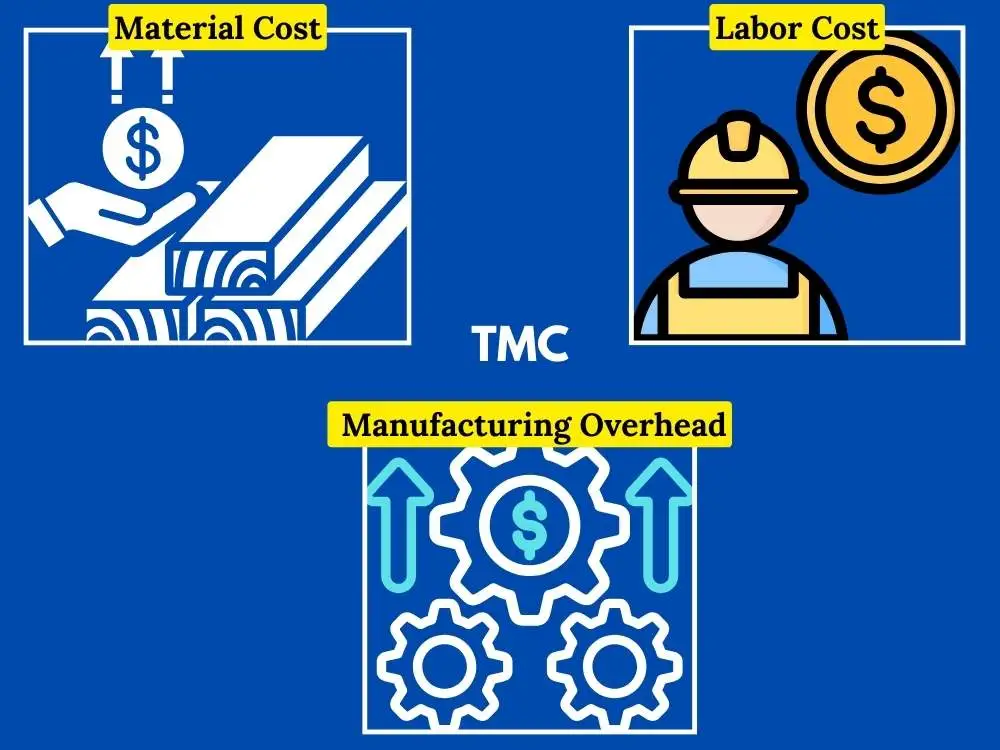
TMC is important because it tells you the true cost of making a product. Without this number, you're more or less flying blind. You would be considering the profits of a given product while lowering the cost, perhaps you're even overcharging, thus driving your customers away.
For manufacturing firms, TMC has a lot of significance, which guides them through various things like pricing, areas of overspending, and possibilities of working smarter. When competitors are breathing down your neck or material cost suddenly goes up, knowing your TMC gives you the power to respond quickly instead of just guessing what to do.
Total Manufacturing Cost Formula
Let's find the standard formula that shows you exactly what makes up your Total Manufacturing Cost:
Total Manufacturing Cost (TMC) = Direct Materials + Direct Labor + Manufacturing Overhead
a) Direct Materials: These are simply all the physical materials that go into your product. Simply they are inputs that are used in the production process. For example, the fabric in your shirts, or the ingredients in your food products. If you can point to it in the finished product, it's probably a direct material.
b) Direct Labor: They are the people who actually make your product. These are your assembly line workers, machine operators, and anyone else directly handling the transformation of materials into finished goods. Their wages, benefits, and related costs all count here.
c) Manufacturing Overhead: It includes all other expenses that are necessary for keeping your factory running but are not directly assigned to specific products. For instance, your factory rent, electricity bills, maintenance costs, salaries for supervisors, depreciation of equipment, or any other operating expenses.
When you add these three together, you get the real cost of what it takes to make your products.
How to Calculate Total Manufacturing Cost (Step-by-Step Guide)
Finding your total manufacturing cost is pretty simple when you've got all the info you need. Let’s check out a simple way to get this done:
Step 1: Identify direct material costs
Prepare a list of all raw materials and components that entered into or became part of your final product. Multiply each by the quantity used and add them up. Do not forget to account for waste and scrap that occur naturally during production.
Step 2: Calculate direct labor costs
Track the hours your production workers spend making your products. Multiply these hours by their hourly wages (including benefits). Only include time spent on actual production and avoid work breaks or administrative tasks.
Step 3: Determine manufacturing overhead
Add together indirect costs related to production, such as payments for factory rent, utilities, maintenance of factory and office, salaries of supervisors, depreciation of production equipment, QC costs, etc. In essence, this category catches everything else closely related to production but not specifically tied to specific units.
Step 4: Now, add up all costs discussed in the previous steps to get the total
Simply add your totals from Steps 1, 2, and 3 to calculate your total manufacturing cost.
Practical Example
Let's say you run a small furniture workshop making wooden chairs:
Direct Materials:
- Wood: $35 per chair
- Screws and hardware: $5 per chair
- Fabric and padding: $15 per chair
- Finishing materials: $7 per chair
- Total Direct Materials: $62 per chair
Direct Labor:
- Each chair requires 2.5 hours of labor
- Production workers earn $20/hour including benefits
- Total Direct Labor: $50 per chair
Manufacturing Overhead:
- Monthly factory rent: $3,000
- Utilities: $800
- Equipment maintenance: $500
- Supervisor salary: $4,500
- Tool depreciation: $700
- Total monthly overhead: $9,500
- Monthly production: 200 chairs
- Overhead per chair: $47.50
Total Manufacturing Cost = $62 + $50 + $47.50 = $159.50 per chair
Total Manufacturing Cost Calculator
Total Manufacturing Cost vs. Cost of Goods Manufactured (COGM)
Many people mix up TMC and COGM. However, they're actually different metrics that tell you different things about your business. Let's see a clear breakdown to understand the difference:
Factor | Total Manufacturing Cost (TMC) | Cost of Goods Manufactured (COGM) |
---|---|---|
Definition | Everything you spent to run production. | The cost of products that were completed during a period. |
Formula | Direct Materials + Direct Labor + Manufacturing Overhead | Beginning WIP Inventory + TMC - Ending WIP Inventory |
Inventory | Doesn't account for work-in-progress (WIP) changes. | Accounts for changes in work-in-progress (WIP) inventory. |
Time Frame | Represents all costs incurred during the period. | Represents costs of goods only that actually completed during the period. |
Purpose | Helps figure out production efficiency and costs. | Connects production to financial statements and inventory valuations. |
Financial Impact | Operating metric for internal decision-making. | Directly impacts balance sheet and income statement. |
Both metrics matter because they give you different insights. TMC helps you understand your actual production costs and efficiency, which makes it crucial for pricing decisions and cost control. On the other hand, COGM connects your production to your financial statements which tells you the real cost of what you finished making during a period.
Think of it this way: TMC shows you what you spent on manufacturing, while COGM shows you what you got for that spending in terms of completed products.
Total Manufacturing Cost Template
How Our Online Tool Can Help
Looking for a faster way to calculate your manufacturing costs? Apart from the above calculator tool, you can also utilize our online tools which can eliminate math headaches and give you accurate average and percentage calculation results.
1) The Average Calculator from Smart Tools AI helps you quickly determine average costs across production runs. This is really useful when your production costs change from one batch to another because of shifting material prices or labor costs. Simply input your cost data from multiple production cycles, where the calculator will generate both the average cost and show you how each batch compares to your typical expenses.
2) Our Percentage Calculator is perfect for breaking down your total manufacturing cost into meaningful percentages. Want to know what portion of your costs goes to materials versus labor? Need to track how overhead expenses change as a percentage of total costs? This tool instantly converts your raw numbers into clear percentage breakdowns, making it easier to spot cost imbalances and opportunities for improvement.
Both tools feature intuitive interfaces that require no special training to use. They're designed to complement the TMC template above, allowing you to perform a deeper analysis of your manufacturing data without complex spreadsheet formulas.
Final Thoughts
Understanding your total manufacturing cost is vital. It's not simply counting things, but rather managing your business cost better. By keeping an eye on direct materials, labor, and overhead costs that form the TMC, you can easily make decisions on pricing while streamlining processes. Also, use our template and calculator to start taking control of your manufacturing costs today.
FAQs
Q1: How often should I calculate my Total Manufacturing Cost?
It’s better you calculate TMC at least once a month which helps keep track of your expenses. Plus, if your material prices or labor costs change frequently, you might want to check them more often.
Q2: Does Total Manufacturing Cost include shipping and distribution costs?
No, TMC only covers the costs of making the product. Shipping and distribution expenses are separate and fall under selling and administrative costs.
Explore Related Posts
https://smarttoolsai.com/post/length-converter-in-apparel-construction-and-other-key-industries